Las resistencias tipo tubular se fabrica utilizando tubing de acero, cobre, acero inoxidable tipo304, 316 e incoloy al cual se le introduce una bobina de níquel cromo centrada y se rellena dicho tubing de óxido de magnesio de alta pureza y se compacta la unidad por medios mecánicos hasta formar un tubo compacto al cual se le puede dar casi cualquier forma, la densidad máxima recomendada es de 65 W/ pulg2 (10 W/cm2 ), pudiendo variar está dependiendo de la aplicación en la que se empleen. Por su versatilidad las resistencias tipo tubular son las más empleadas en cualquier industria, desde las muy especializadas hasta las más sencillas, ya que por su diseño las resistencias tipo tubular producen un calefactor robusto, confiable y durable ya que resiste choques, vibraciones, corrosión y altas temperaturas.
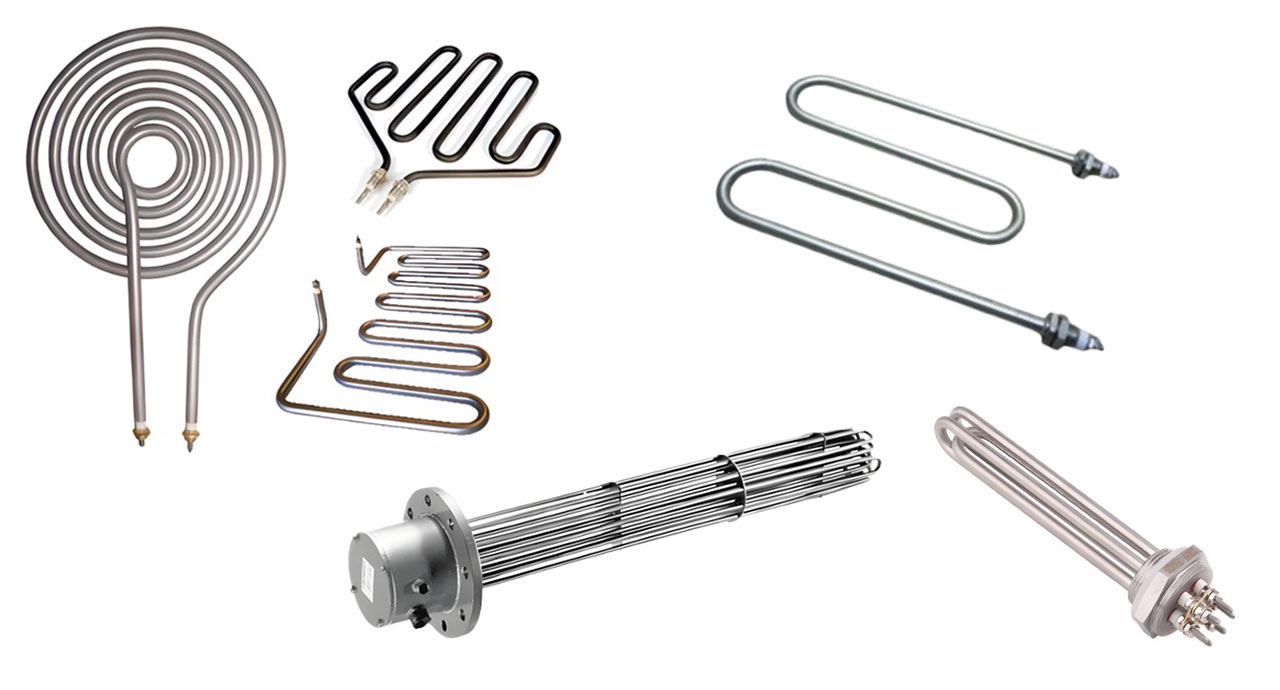
Como ya se menciona anteriormente las resistencias tipo tubular se pueden ofrecer desde su forma más sencilla es decir en forma recta con diámetros que van de ¼” (6.35 mm.), 5/16” (7.93 mm), 3/8” (9.52 mm), 7/16” (11.1 mm), ½” (12.7 mm) ,5/8” (15.87 mm)
O elaborar la figura más caprichosa que se pueda imaginar. Otra de las muchas aplicaciones de las resistencias tipo tubular es que se pueden sumergir en casi cualquier líquido que se requiera calentar de forma directa, para tal efecto las resistencias tipo tubular se pueden soldar con plata o alguna aleación compatible con el material de la resistencia a varios tipos de conexiones, bridas, placas o medio de sujeción para poder sumergirlas pudiendo soldar una, dos o grupos de tres elementos pudiendo formar bancos de resistencias de hasta 78 elementos sin ser lo anterior el máximo posible.
Disponibles con cajas de protección a las terminales según la necesidad del cliente cumpliendo con las normas NEMA para tal efecto, así como es posible colocar controles de temperatura tipo termostato en la misma caja de protección o soldar termopozos para insertar termopares. Por ser tan versátiles no se les puede dar una aplicación específica pero dentro de las más usuales son: Para las resistencias tubulares que trabajan al aire se puede combinar el efecto de radiación y convección con solo sujetar adecuadamente la resistencia a la pieza a calentar para tener magníficos resultados. Así mismo si se requiere calentar aire con solo colocarle aletas de disipación a las resistencias se puede hacer circular aire forzado dentro de un ducto y se obtendrán los resultados esperados